Zirconia exists in three major phases: monoclinic, tetragonal, and cubic. Monoclinic is room-temperature stable.5 Above 1170°C, zirconia transforms into the tetragonal intermediate phase; at 2370°C, the material changes into a cubic phase. In pure zirconia ceramics, the cubic-to-monoclinic phase transformation occurs during cooling with approximately 5% volumetric expansion (causes cracks), which may then fracture zirconia at room temperature. Therefore, biomedical and structural/functional applications of zirconia typically do not use pure zirconia. The addition of other ceramic components may alter the presence and stability of these phases at room temperature. Zirconia may exist primarily in the tetragonal phase at room temperature by adding components such as calcia (CaO), magnesia (MgO), yttria (Y2O3), and ceria (CeO2). If the right amount of component is added, then a fully stabilized cubic phase (cubic zirconia) can be created. The addition of smaller amounts (3 weight% to 5 weight%) produces a partially stabilized zirconia. Although stabilized at room temperature, the tetragonal zirconia phase may change under stress to monoclinic with a subsequent 3% volumetric increase.6 This dimensional change diverts energy from the crack and can stop the crack. This is called transformation toughening This helps resist catastrophic failure—even though a crack may exist in the material, the phase change prevents it from proceeding throughout the restoration. Yttria-stabilized tetragonal zirconia polycrystal (Y-TZP) has the potential to be a “universal” ceramic restorative material in that it has sufficient properties to withstand stresses in all regions of the mouth, as well as the ability to support multiple-unit restorations.
Most restorations containing zirconia frameworks are fabricated by machining a porous or partially fired block of zirconia. The framework is milled oversized and then fired at approximately 1500°C to fully densify the zirconia, producing a translucent material and strength values from 900 MPa to 1200 MPa. Most blocks have barcodes that tell the computer the density in order to properly mill the framework.
The use of zirconia for dental restorations in 2009 was about 50% of all restorations made completely from a ceramic. As the popularity has increased, so too has the number of suppliers of machinable blocks. There are many “brand name” manufacturers with reliable products, but there are also many questionable blocks being sold. Differences among zirconia ceramics can occur with the level of zirconia purity, grain size, trace elements, and stabilizing compounds. There are differences in the zirconia starting powders and the processing of those powders into blocks. Consequently, clinical outcomes, such as marginal fit, translucency, strength, and long-term stability, can be significantly affected. Zirconia may degrade over time.9,10 However, accelerated aging tests in steam and boiling water of two manufacturers’ zirconia products (Lava™, 3M ESPE Vita In-Ceram YZ, Vita Zahnfabrik, found no degradationOther zirconia block materials may show degradation. A batch of hip implants manufactured by Saint Gobains failed catastrophically after a few years in patients’ bodies.This may have been due to a problem with the exact composition of the zirconia in regard to the amount of yttria and alumina, leading to uncontrolled phase transformation. To help prevent instability of the crystal phases, zirconia formulations should have a small amount of alumina.

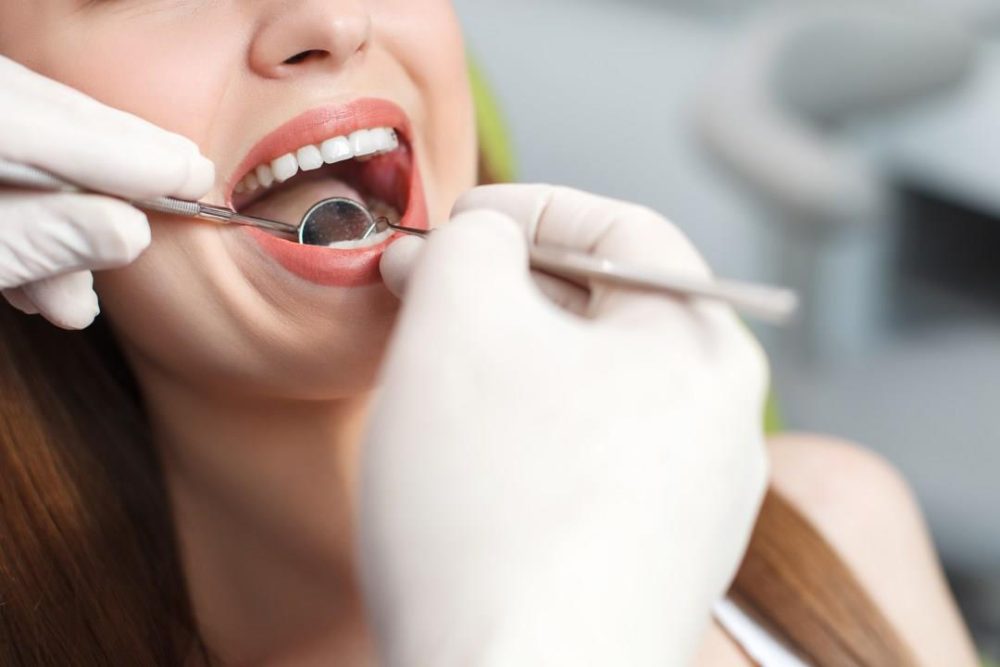
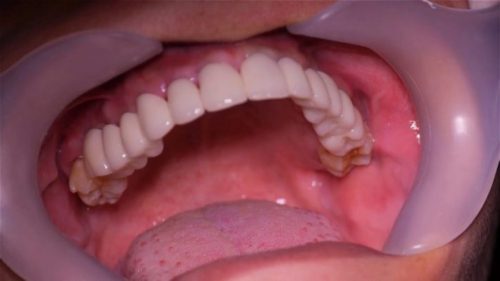
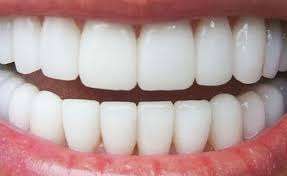